|
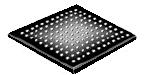 |
|
BGA Solder Ball |
|
Standard Lead Free Alloy RoHS (Pb Free) |
Ref. |
Composition |
Solidus °C |
Liquidus °C |
Density gm/cc |
SAC305 |
Sn96.5 Ag3.0 Cu0.5 |
217 |
220 |
7.4 |
 |
Minimum Order 250K pcs |
|
|
Special Lead Free Alloy RoHS (Pb Free) |
Ref. |
Alloy |
Solidus °C |
Liquidus °C |
Density gm/cc |
SAC101 |
Sn98.9 Ag1.0 Cu0.1 |
- |
- |
7.343 |
SAC105 |
Sn98.5 Ag1.0 Cu0.5 |
215 |
227 |
7.350 |
SAC125 |
Sn98.3 Ag1.2 Cu0.5 |
- |
- |
7.356 |
SAC125+Ni |
Sn98.25 Ag1.2 Cu0.5 Ni0.05 |
- |
- |
7.356 |
SAC266 |
Sn96.8 Ag2.6 Cu0.6 |
- |
- |
7.403 |
SAC300 |
Sn96.95 Ag3.0 Cu0.05 |
- |
- |
7.406 |
SAC302 |
Sn96.8 Ag3.0 Cu0.2 |
217 |
220 |
- |
SACN306 |
Sn96.3 Ag3.0 Cu0.6 Ni0.04 |
220 |
226 |
~7.4 |
SAC307 |
Sn96.3 Ag3.0 Cu0.7 |
- |
- |
- |
- |
Sn80.8 Sb18 Ni.2 |
- |
- |
- |
SAC350 |
Sn96.45 Ag3.5 Cu0.05 |
- |
- |
7.422 |
SAC357 |
Sn95.8 Ag3.5 Cu0.7 |
217 |
218 |
7.4 |
SAC387 |
Sn95.5 Ag3.8 Cu0.7 |
217 |
218 |
7.442 |
SAC400 |
Sn95.95 Ag4.0 Cu0.05 |
- |
- |
7.438 |
SAC396 |
Sn95.5 Ag3.9 Cu0.6 |
217 |
218 |
7.4 |
SAC405 |
Sn95.5 Ag4.0 Cu0.5 |
217 |
225 |
7.445 |
Sn96 |
Sn96.5 Ag3.5 |
- |
- |
7.400 |
SACQ |
Sn92.45 Ag4 Cu0.5 Bi3.0 Ni0.05 |
207 |
217 |
NA |
Innolot |
~Sn92.3 Ag3.8 Cu0.7 Bi2.0
Sb1.0 Ni0.2 |
206 |
218 |
7.4 |
iSAC |
Sn93.44 Ag4.2 Cu0.9 Bi1.3 Ni0.08 Zn0.05 Ge0.3 |
- |
- |
NA |
PF925S |
Sn89.2 Ag3.5 Cu0.8 Bi0.5 In6.0 |
202 |
204 |
7.4 |
 |
Minimum Order 250K pcs |
|
|
Non Lead Free Alloy |
Ref. |
Composition |
Typical Device Types |
Available Special Order |
Density gm/cc |
Sn62 |
Sn62 Pb36 Ag2.0 |
BGA/CBGA |
Yes |
8.44 |
Sn63 |
Sn63 Pb37 |
BGA |
Standard |
8.4 |
Sn60 |
Sn60 Pb40 |
N/A |
No |
8.5 |
Sn20 |
Sn20 Pb80 |
CCGA |
Column |
10.2 |
Sn15 |
Sn15 Pb85 |
CCGA |
Column |
10.5 |
Sn10 |
Sn10 Pb90 |
CBGA CCGA |
Ball Column |
10.7 |
Sn5 |
Sn5 Pb95 |
Flip Chip |
Ask |
11.0 |
 |
MOQ = Minimum Order 250Kpcs |
|
|
Indium Alloy |
Ref. |
Composition |
Typical Device Types |
Available Special Order |
Density gm/cc |
In50 |
In50 Sn50 |
BGA/CBGA Cold Electronics |
Yes |
7.29 |
In50Pb |
In50 Pb50 |
BGA/CBGA Cold Electronics |
Yes |
8.86 |
In52 |
In52 Sn48 |
BGA/CBGA Cold Electronics |
Yes |
7.29 |
In60Pb |
In60 Pb40 |
BGA/CBGA Cold Electronics |
Yes |
8.52 |
 |
MOQ = Minimum Order 50Kpcs |
|
|
Ball Diameter |
Ø Ball Dia (mm) |
Ø Ball Dia (Mil) |
Standard BGA Pitch |
Alternative BGA Pitch |
Ø Ball Diam Tolerance Pre-Reflow |
0.10mm |
4mil |
- |
- |
±5µm |
0.15mm |
6mil |
- |
- |
±10µm |
0.20mm |
8mil |
0.3mm |
- |
±10µm |
0.25mm |
10mil |
0.4mm |
- |
±10µm |
0.30mm |
12 mil |
0.5mm |
- |
±10µm |
0.35mm |
14 mil |
0.65 ~ 0.75mm |
- |
±10µm |
0.40mm |
16 mil |
0.8mm |
1.0mm |
±10µm |
0.45mm |
18 mil |
0.8mm |
1.0mm |
±10µm |
0.50mm |
20 mil |
1.0mm |
0.8mm |
±10µm |
0.61mm |
24 mil |
1.0mm |
- |
±15µm |
0.63mm |
25 mil |
1.0mm |
- |
±15µm |
0.76mm |
30 mil |
1.27 ~ 1.5mm |
- |
±15µm |
 |
Other Ball Diameters Avialable:
|
|
|
Ball Weight (Mass) |
Ø Ball Dia (mm) |
Ø Ball Dia (Mil) |
Solder ball Volume cm3 |
Quantity Balls Per gm Sn63/Pb37 |
Quantity Balls Per gm SAC305 |
0.10mm |
4mil |
5.236*10-7 |
227,000 |
258,000 |
0.15mm |
6mil |
1.767*10-6 |
67,000 |
76,000 |
0.20mm |
8mil |
4.189*10-6 |
28,000 |
32,000 |
0.25mm |
10mil |
8.181*10-6 |
14,500 |
16,500 |
0.30mm |
12 mil |
1.414*10-5 |
8,400 |
9,500 |
0.35mm |
14 mil |
2.245*10-5 |
5,300 |
6,000 |
0.40mm |
16 mil |
3.351*10-5 |
3,500 |
4,000 |
0.45mm |
18 mil |
4.771*10-5 |
2,500 |
2,800 |
0.50mm |
20 mil |
6.545*10-5 |
1,800 |
2,060 |
0.61mm |
24 mil |
1.188*10-4 |
1,000 |
1,130 |
0.63mm |
25 mil |
1.309*10-4 |
910 |
1,030 |
0.76mm |
30 mil |
2.230*10-4 |
520 |
590 |
 |
Above table shows the number of balls contained in 1 gram of weight (mass).
The Mass (gm) of an individual solder ball is calculated by dividing the number of balls into the number 1.0 Example: 1/590 = 0.001695gm is the mass of a single SAC305 ball measuring Ø 0.76mm diameter Weights and measurements provided above are approximations and are not guaranteed to be accurate. Numbers are rounded or truncated for easy reference.
|
|
|
Maximum Mechanical Downward Pressure (Force) on Top of BGA |
Ø Ball Dia (mm) |
Ø Ball Dia (Mil) |
Pitch Solder Ball Spacing |
Max Pressure Per Ball Sn63/Pb37 |
Max Pressure Per Ball SAC305 |
0.25mm |
10mil |
0.5mm |
3 g |
7 g |
0.40mm |
16 mil |
0.8mm |
6 g |
12 g |
0.50mm |
18 mil |
0.92mm Hex Pattern |
7 g |
14 g |
0.63mm |
25 mil |
1.0mm |
8 g |
16 g |
0.76mm |
30 mil |
1.27mm |
12 g |
24 g |
 |
Maximum mechanical downward pressure (force) caused by heatsink mass mounted on top of BGA.
PCB and BGA should be designed to prevent bending or flexing of the PCB and BGA substrate.
Pressure is typically applied to a thermal pad to keep contact between the top of the BGA and underside of heatsink.
The pressure should be limited to prevent the BGA from being destroyed by too much force on top of the package.
Above data was extracted from recommendations provided by Intel (Altera) as of May 2020.
Data provided above are approximations and are not guaranteed to be accurate.
Numbers are rounded or truncated for easy reference. |
|
|
Solder Ball Tolerance (Before Reflow) |
Ø Ball Dia (mm) |
Ø Ball Dia (Mil) REF |
Dimensional Tolerance Before Reflow |
0.10mm |
4mil |
±5um |
0.125mm |
5mil |
±5um |
0.15mm |
6mil |
±10um |
0.20mm |
8mil |
±10um |
0.25mm |
10mil |
±10um |
0.30mm |
12 mil |
±10um |
0.35mm |
14 mil |
±10um |
0.40mm |
16 mil |
±10um |
0.45mm |
18 mil |
±10um |
0.50mm |
20 mil |
±10um |
0.61mm |
24 mil |
±15um |
0.63mm |
25 mil |
±15um |
0.76mm |
30 mil |
±15um |
 |
Solder ball tolerance is applicable before use (before reflow).
Solder ball tolerance after use (after relow) is not defined.
Roundness of the ball is affected by the pad diameter, soldermask (SMD or NSMD) and downward pressure during reflow.
Data provided above are approximations and are not guaranteed to be accurate.
|

TopLine Corporation
95 Highway 22 W
Milledgeville, GA 31061, USA
Toll Free USA/Canada (800) 776-9888
International: 1-478-451-5000
Email: Info
©2021 TopLine. All Rights Reserved.
|
Home
|
|